Basic Info.
Model NO.
PSK-106
Mould Cavity
Multi Cavity
Plastic Material
POM
Process Combination Type
Single-Process Mode
Application
Car, Household Appliances, Electronic, Home Use, Hardware
Runner
Hot Runner
Design Software
UG
Installation
Fixed
Certification
TS16949, CE, ISO
Standard
HASCO
Customized
Customized
After-sales Service
3 Years
Transport Package
Wood or Customized
Specification
58x48x36cm
Trademark
PSM
Origin
China
HS Code
3901100001
Production Capacity
600set/Years
Packaging & Delivery
Package Size
58.00cm * 48.00cm * 36.00cm
Package Gross Weight
350.000kg
Product Description
Products Information | ||
Product Name | Auto Moulded Parts Bumper Plastic Mold | |
Shaping Mode | Plastic Injection Mould | |
Surface treatment | Polish. Etched. Texture | |
Ejection System | Ejector pin | |
Part Material | ABS | |
Part Size(MM) | 580*480*360 | |
Mold Standard | HASCO standard | |
Packaging | According to customers' requirement | |
Mould Steel | A plate | S50C |
B plate | S50C | |
Cavity Insert | S136 (HRC 45-50 ) | |
Core Insert | S136 (HRC 45-50 ) | |
Slider Insert | 2344 | |
Ejector Plate | S50C | |
Spare Parts | S50C | |
Mould Description | Mould Size(L*W*H MM) | 980*860*450 |
Mould Gross Weight(KGS) | 965 | |
Mould Life Time(Shots) | 1,000,000 | |
Mould Manufacturing Cycle | 35 days | |
Surface Finish | Polishing | |
Runner Description | Hot runner | |
Ejection System | Eject blade | |
Cycle Time(Second) | 55s | |
Injection Gate Type | Side gate |
Mould Type | Plastic Injection Mold |
Mould Material | P20/718/738/NAK80/S136 |
Mould Base | HASCO,DME,MISUMI,JIS,LKM etc |
Mould Runner | Cold Runner/ Hot Runner |
Mould Gate | Slide Gate/Sub Gate/Pin- point Gate |
Cavity | Single /Multi Cavity |
Designing Software | UG/PROE/CAD/SOLIDWORKS |
Moulding equipment | CNC,Wire Cutting,Milling Machine,EDM |
Raw-material | ABS,PP,PC,PA6,PA66,PVC,POM,PMMA,PS etc |
Package way | Wooden pallet, carton |
OEM/ODM | Welcome and please offer 2D/3D file or sample |
Lead time | About 20 days |
Design of Injection Mould for Automobile Steering Wheel
The steering wheel of a car is a plastic part of the car interion.In industry,steering wheels are mass-produced by injection molds.The interior parts of automobiles are mainly plastic parts,and the quality of injection molds is an important factor affecting the interior of automobiles.Therefore,it is of practical significance to study the mold design of interion parts of automobiles."Steering wheel injection mold design" is designed by Pro/E software.
Steering Wheel Material Properties
The material of plastic parts is ABS,an engineering plastic with good comprehensive properties.It has good processing and molding properties,excellent dimensional stability,high impact strength and good appearance characteristics.Properly increasing the mold temperature can improve the smoothness of the plastic parts.The material density is 1.02-1.05g/cm3(injection grade density is 1.05g/cm3),the theoretically calculated shrinkage rate is 0.6%,and the flash value is 0.04mm.
Steering Wheel Injection Mold Design Steps
Parting Design
When establishing the parting surface,the steering wheel injection mold design first establishes the parting surface for one mold one cavity,divides the volume block and casts the mold for one mold and one cavity,and then established the parting surface of one mold and two parts.In the parting process,the left and right corners of the plastic part are the most complicated.These two parts are the intersection of the parting surfaces,and there is a certain gap between the parting surfaces.Therefore,the general parting method is used.The volume block can not be divided,and the total parting surface can not be obtained.The steering wheel injection mold is designed by selecting the modeling line on the product to project it onto the workpiece,and then strectching the projection line through the upper surface of the product to become a polygonal parting surface,and finally merging all the side parting surfaces.This mold is a one-piece two-piece layout,so the boundary mixing method is used to establish the parting surface between the two parts,and then all the parting surfaces are merged to establish the total parting surface.Steering Wheel Injection Mold Gate Design
Since the side gate is generally opened on the parting surface and the material is fed from the outer side of the plastic part,the gate cross-sectional shape is simple,the processing is convenient,the traces left on the plastic part are small,and the molding can be ensured well,so according to the plastic part structural features,the steering wheel injection mold design selects the side gate.When determining the position of the gate,the gate should be designed at the thickest part of the product wall,and the distance from the gate to the various parts of the cavity should be as close as possible to facilitate feeding;avoid spraying at the gate,which may occur during molding.Snake flow,and the gate should be designed to be the main force when the product is formed.
Steering Wheel Injection Mold Cooling System
The cooling system should be installed as close as possible to the cavity without interfering with the ejector system and other connecting parts.According to the structural complexity of the plastic parts,the cooling water channel can be a straight-through type or a rotary type.The straight-through water channel has a simple structure and is easy to process,but the cooling effect is general.The path of the rotary water channel is closer to the contour of the cavity,and the cooling effect is better,but the processing cost is high,and sometimes a split structure must be used.The design of the steering wheel injection mold adopts a straight-through cooling water channel,and the cooling water channels of the movable mold and the fixed mold are arranged as shown in the cooling water channel diagram.By adjusting the flow of cooling water,the heat dissipated by the cooling system can be controlled,thereby adjusting the temperature of the mold cavity.
Steering Wheel Injection Mold Work Process
After the mold is closed,the injection molding machine begins to inject ABS material into the cavity,and after a period of pressure-holding molding,the movable mold begins to separate from the fixed mold along with the injection molding machine.Under the action of the action and the core wrapping force,the plastic parts and the flowing condensate remain on the movable mold.Under the action of the ejector mechanism,the plastic parts are separated from the movable mold.Under the action,the ejector rod returns to the position where the mold was closed,and finally the mold is closed.At this point,the mold has completed a working cycle.
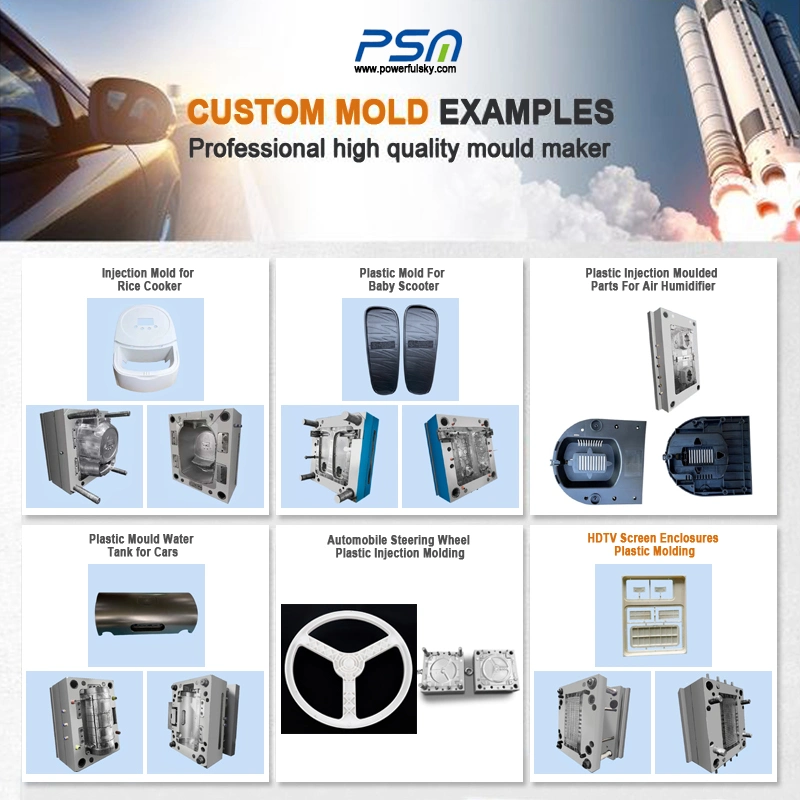
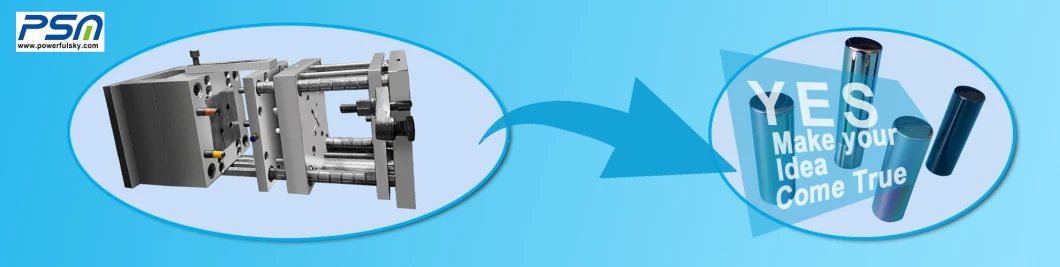
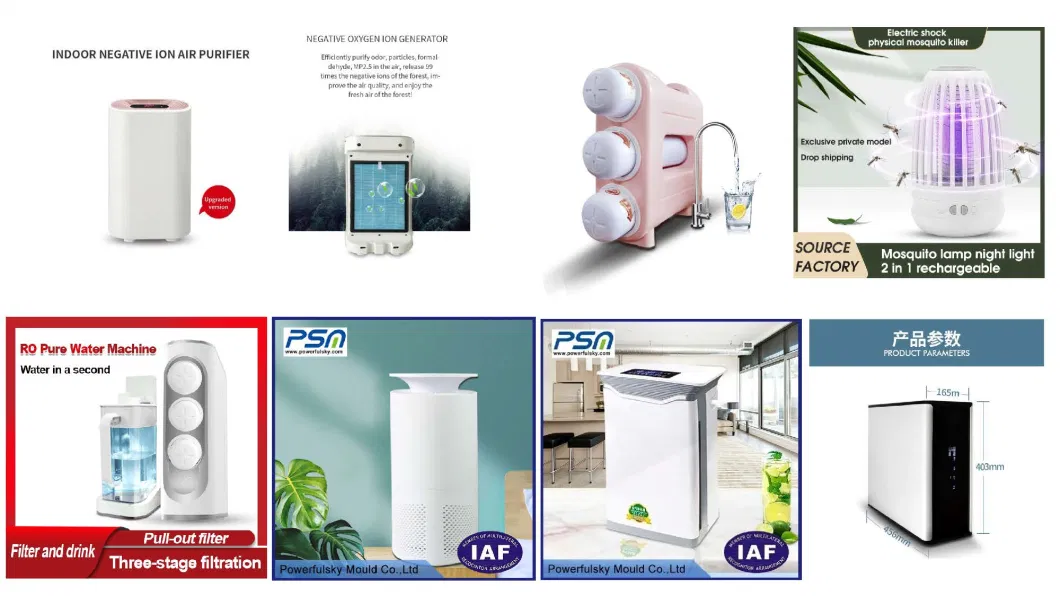
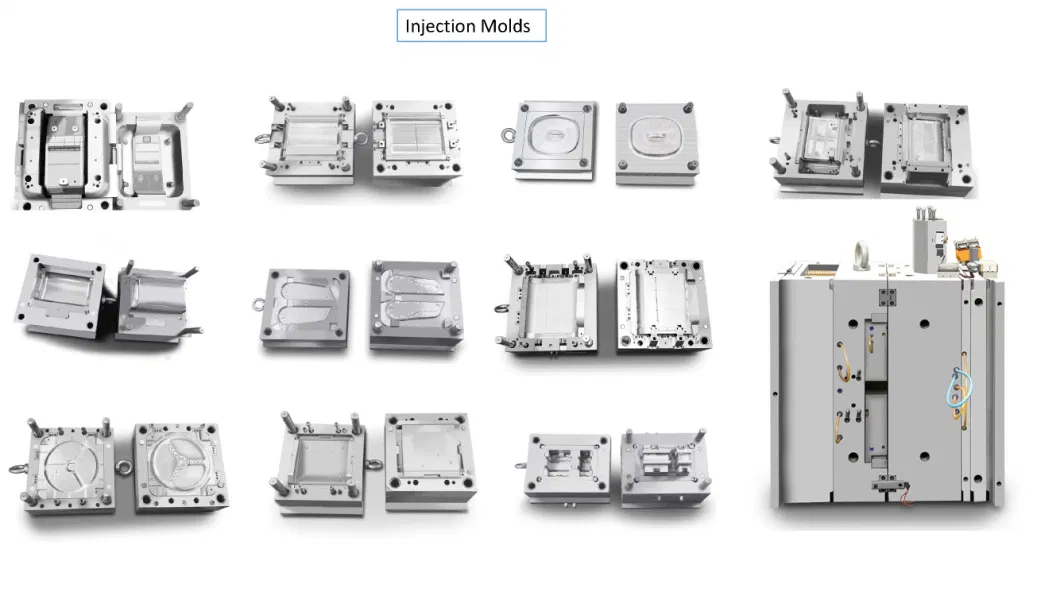
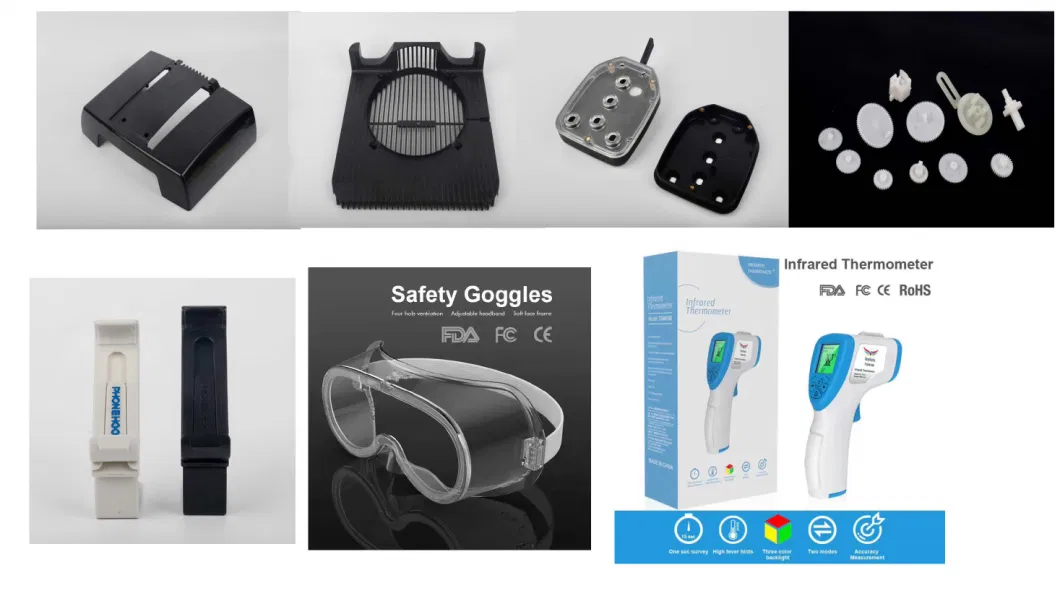
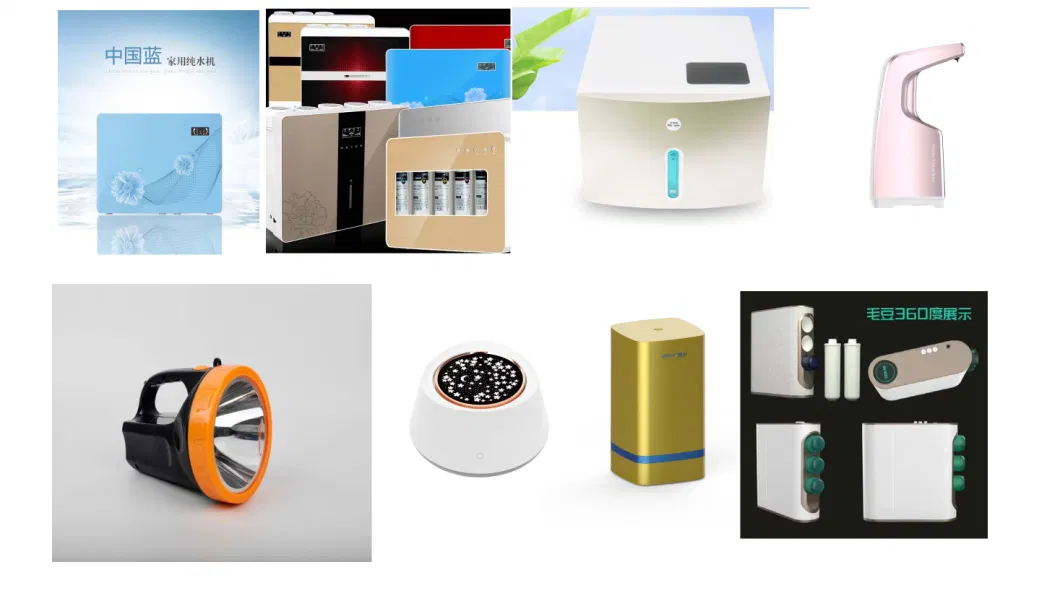
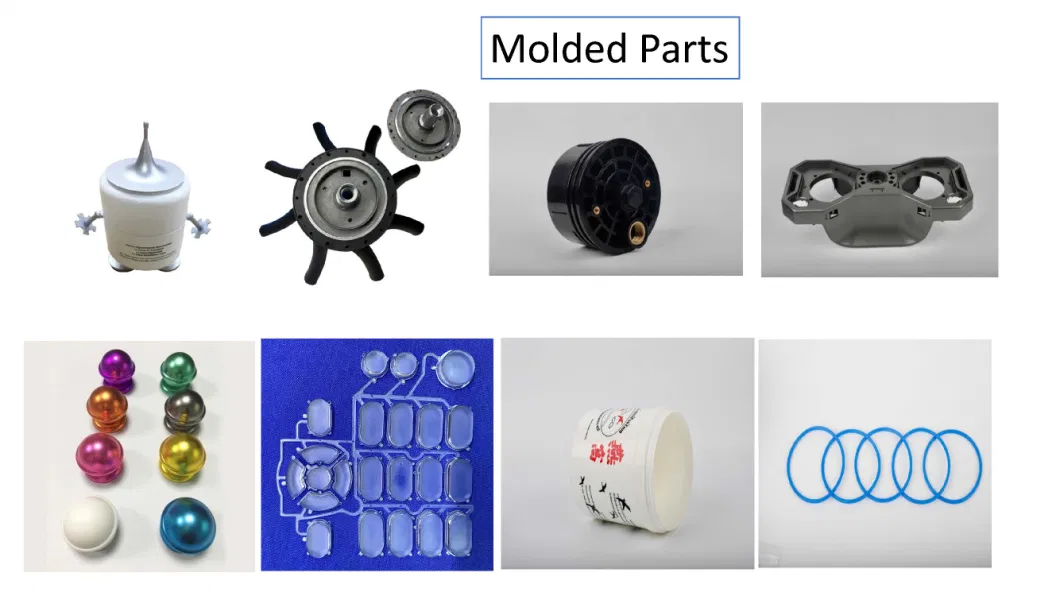
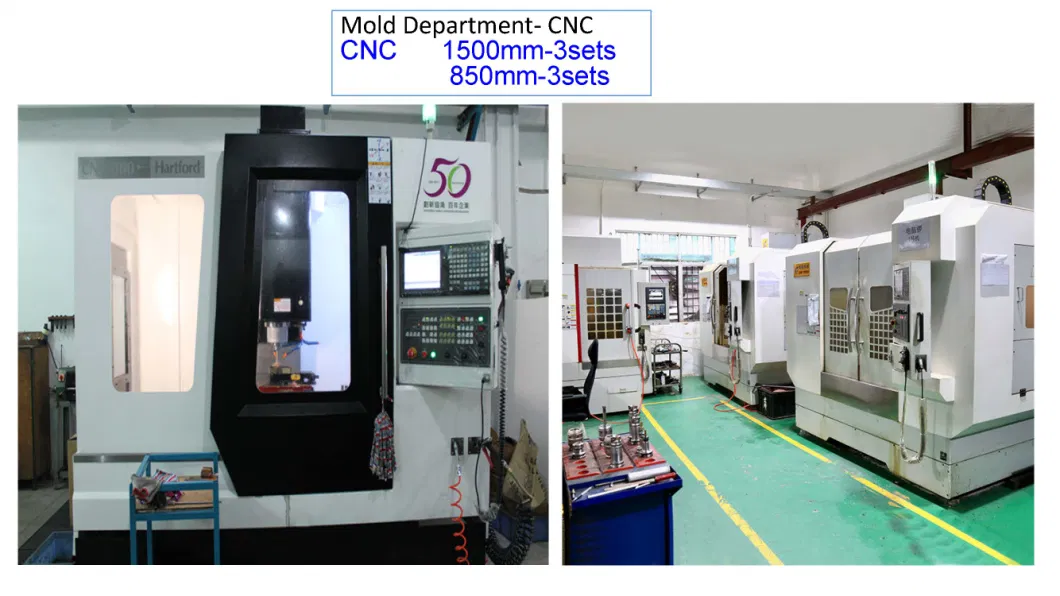
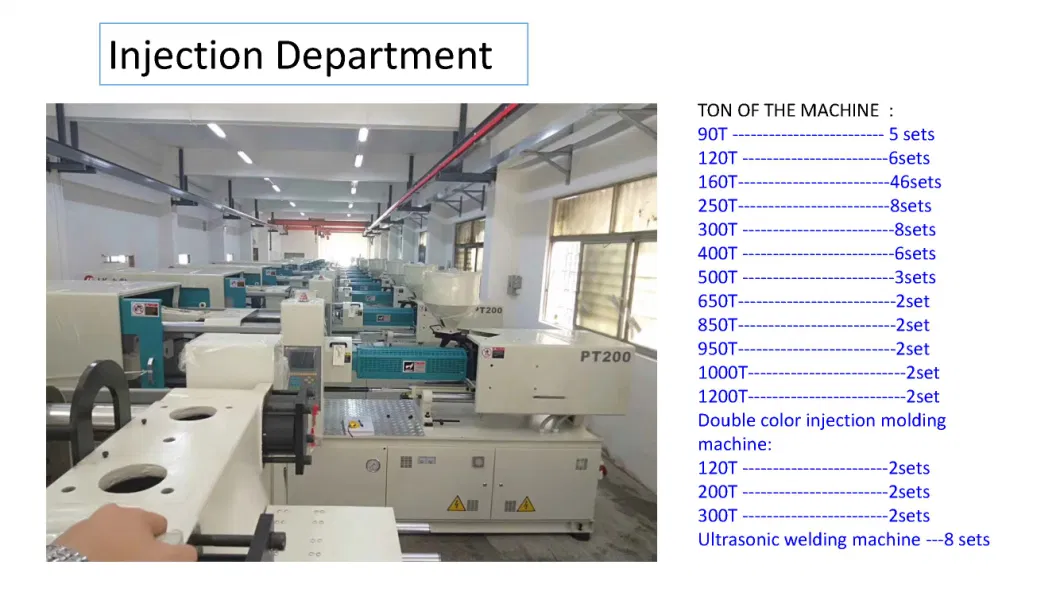
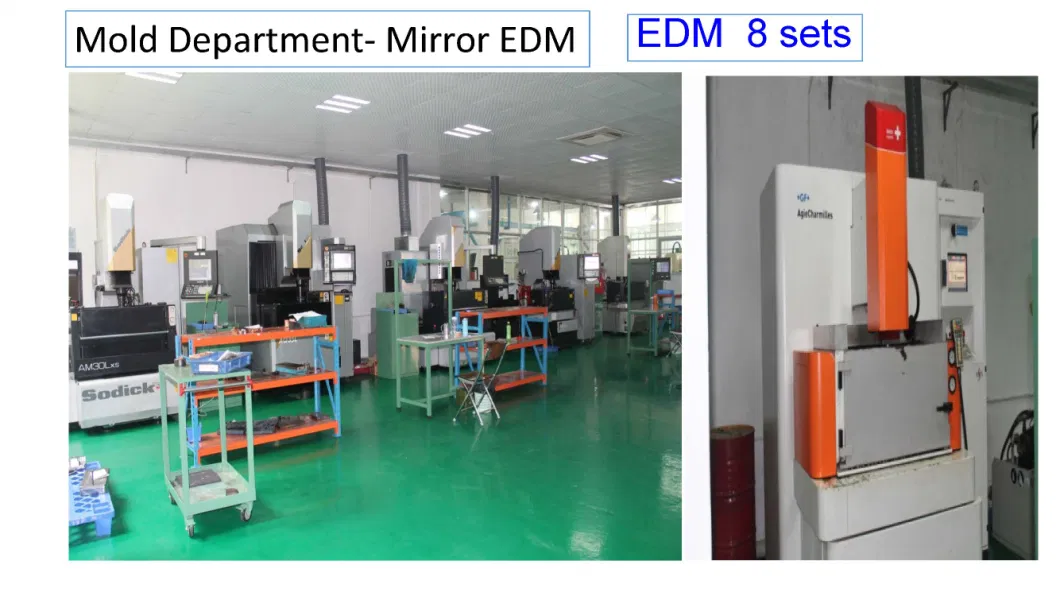
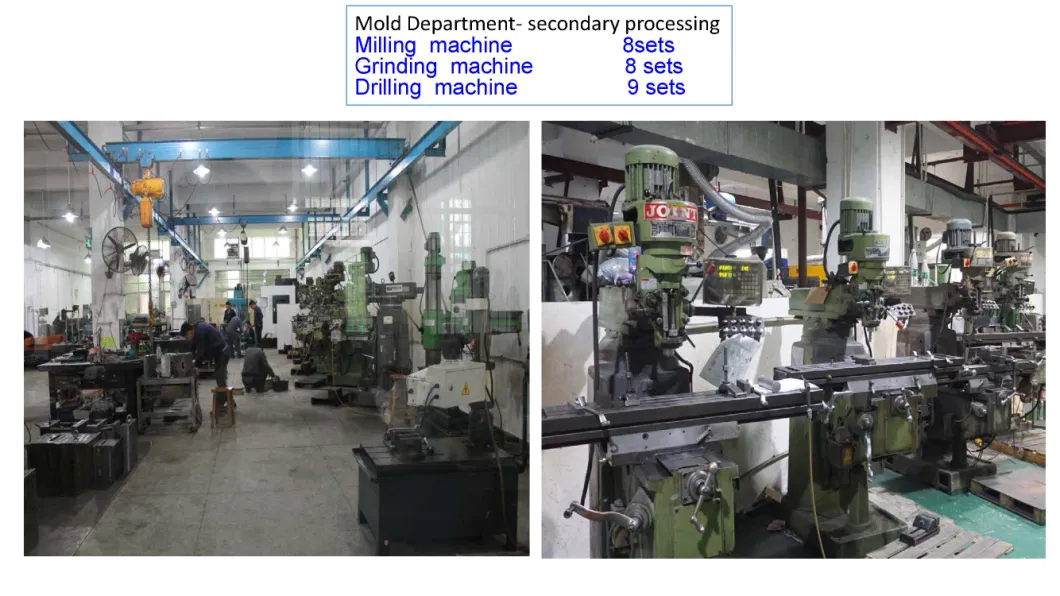
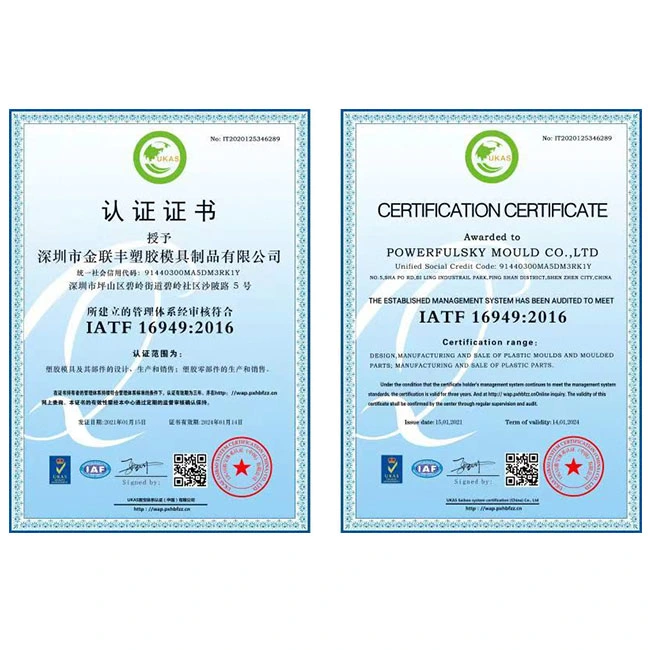
FAQ
Q: When can I get the price?
A: We usually quote within 24 hours after we get your inquiry.If it is very
Urgent,please call us or tell us in your email so that we will regard your Inquiry as priority.
Q:How long is the lead time for mold?
A:It depends on the mold's size and complexity.Normally,the lead time
Is 25~35 days.If the olds are very simple and not in big size,we can work out with 10 days.
Q:Will my drawings be safe after sending to you?
A:Yes,we will keep them well and not release to the third party without your permission.
Q:How to respond quickly to products?
A:If you contact us by email,Wechat,Whatsapp,we promise to reply you within 8 hours.
OEM/ODM
If you ...
1. Are looking for OEM/ODM manufacturers in this industry.
2. Need someone that can produce what you want and have a custom design printed to your specification.
Then our OEM/ODM service is for you!