- Overview
- Product Description
- Certifications
- Company Profile
- Our Advantages
- FAQ
- Packaging & Shipping
Basic Info.
Packaging & Delivery
Product Description
1 | Mould Base | LKM, DME, HASCO etc ; |
2 | Cavity Material | 1.2738,1.2343, 1.2344, S7, H13, P20, P20HH, GS738H, LKM738H, 718, 8407, S136, Calmax 635, NAK80, SKD-61,NIMAX, 45#, 50#, Aluminum for prototype mold etc. |
3 | Steel Hardness | HRC 20-60 |
4 | Treatment | Pre-Harden, Nitride, Heat treatment, Quenching |
5 | Cavity Qty | Single-cavity / Multi-cavity |
6 | Runner | Cold runner or Hot runner :YUDO/ HUSKY/ MOLD-MASTERS/ SYNVENTIVE/ INCOE/ MASTIP/ HASCO/ DME |
7 | Gate | Submarine gate, tunnel gate, side/edge gate, direct gate, pin point gate, sprue gate, diaphragm gate, fan gate, cashew gate, hook gate, hot tip, hot drop, valve gate etc. |
8 | Plastic material for parts | PS, SAN, PA, POM, ABS, PP, PET, PC, PE, HDPE, PA66+GF, NYLON 6/66, PPSU, PEEK, PVC, TPE, TPU, TPV etc |
9 | Mould Life | 50K - 1 million cycles |
10 | Design Software | UG, CAD, PRO-E, Solid Works etc, |
11 | Process | CNC, high speed carve, EDM ,wiring-cutting, drill, polish etc |
12 | Quality | ISO9001:2000 Certified |
13 | Lead Time | 10-30 work days depends on the structure and size of products |
14 | Package | Wooden Case Package or according to customer requirement |
15 | Price Term | EX Works, FOB Shenzhen, FOB Hong Kong, China, CFR, CIF, DDU, DDP |
16 | Payment | T/T, Western Union , Money Gram |
17 | 20 years professional manufacturing experience, specialized in design and manufacture of plastic injection mould ( tooling) for Automotive, Electrical appliances ,House wares , Medical devices, Toys and Games, Communication industries and etc. | |
18 | OEM & ODM orders are welcome. |
Win Win Industrial (Shenzhen) Co., Limited was established in 2006 and has since become a leading provider of comprehensive "turnkey" services in the manufacturing industry. Our expertise includes product design, prototype parts production, mold design, mold manufacturing, plastic injection molding, automotive checking fixtures, and more.
We specialize in designing and producing a wide range of Plastic Injection Molds, catering to various needs:
- Multi-Cavity Molds
- 2-Shot / Multi-Material Molds
- Over Mold
- Unscrewing Molds
- Insert Molds
- Stack Molds
- Cold Runner, 3-Plate, Semi-Hot, and Full Hot Runner Molds
- Rapid Prototyping Molds
- Large size molds
- Gas Assist Molds
- In Mold Labelling IML / In Mold Decoration IMD
- Die Casting tools
- Automotive Checking Fixture
Plastic Injection Molding Production
- On-site injection plastic mold repair & maintenance
- Injection machines ranging from 80 - 600 tons
- 24-hour plastic molding manufacturing shifts
- Long and short plastic injection molding production runs
- Insert molding, dual-color molding service
- General resin and industrial plastic such as ABS, PP, PE, HDPE, LDPE, PC, PC+ABS, POM, ***, PA66+33%GF, PPT, PVC, etc.
Win Win Mold, a division of Win Win Industrial (Shenzhen) Co., Limited, is a full-service Plastic Injection Molding manufacturer specializing in custom manufacturing. Our experienced tool makers and setters ensure optimal product output in minimal time. Your product is molded to your specifications and undergoes rigorous quality inspections to guarantee accuracy and quality at all times.
Our molds and products cater to a diverse range of industries, including Automotive, Household electrical appliances, Electronics, Medical, Packaging, Telecommunications, and Industrial tools. Let the Win Win team support you in making your next project a resounding success!
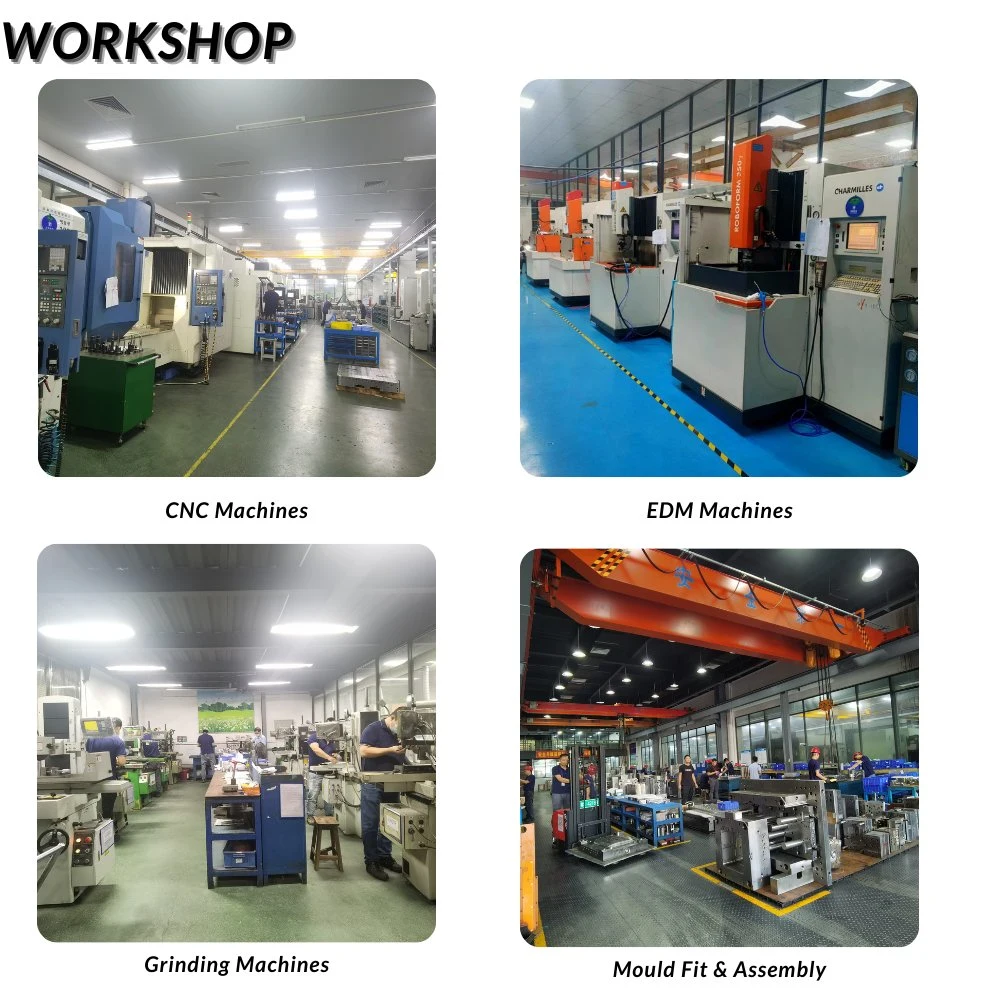
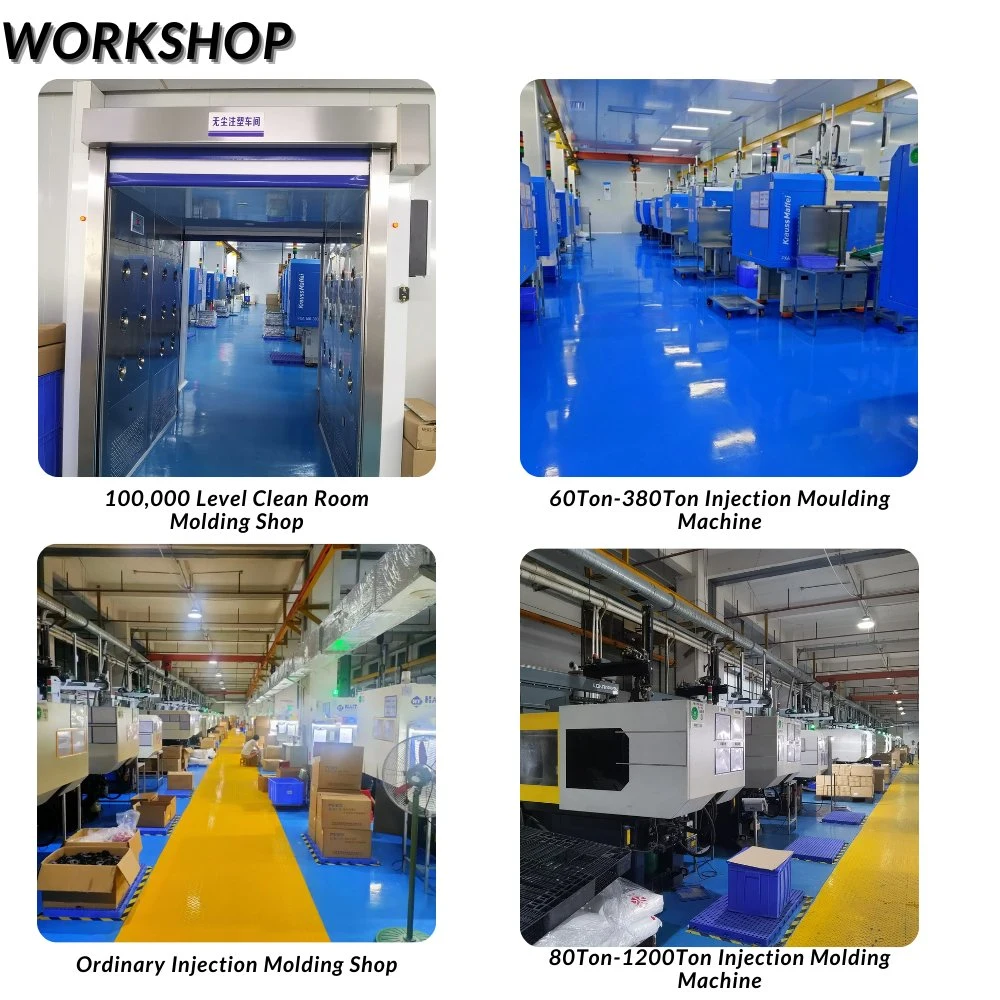
Win Win Mold - Quality Molds for Quality Parts
Engineering Capability
Win Win Mold's engineering team utilizes advanced CAD/CAE/CAM design and processing systems to create high-quality molds. Our engineers work closely with customers to develop well-designed molds that are easy to maintain and cost-effective to produce.
Project Management Process
Our project management process ensures timely delivery of molds and products with superior quality. From project input to final inspection, our team provides detailed reports and updates to keep customers informed throughout the process.
Quality Control
Quality is our top priority at Win Win Mold. We implement rigorous quality control measures at every stage of production to ensure that our tooling meets the highest standards and consistently delivers quality parts with minimal cycle time.
- Mold Design Control
- Mold Steel Hardness Inspection
- Mold Electrodes Inspection
- Mold Core and Cavity Steel Dimension Inspection
- Mold Pre-Assembly Inspection
- Mold Trial Report and Samples Inspection
- Pre-Shipment Final Inspection
- Export Product Package Inspection
With our dedicated QA team and state-of-the-art equipment, we guarantee the quality of your projects and ensure that our tooling meets your specifications.
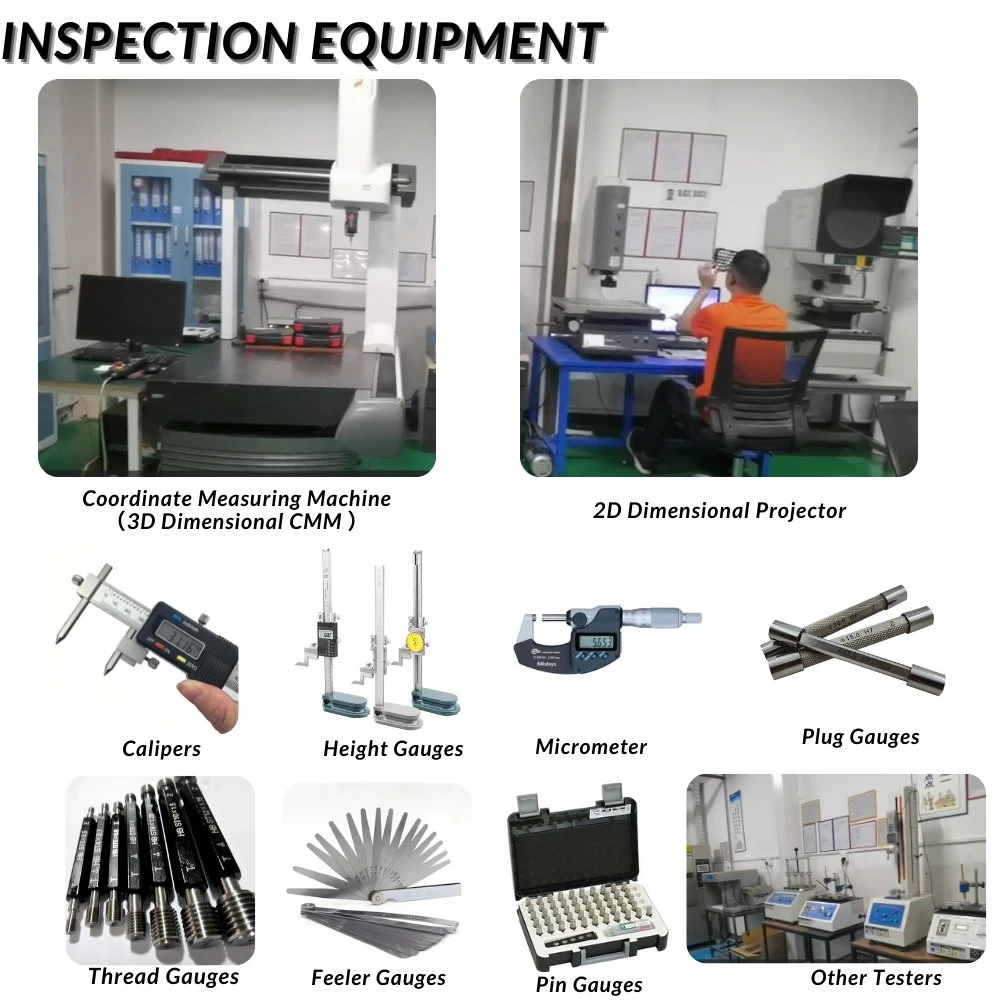
FAQ:
Q. I have an idea for a new product, but I don't know if it can be manufactured. Can you help?
A. Yes! We are always happy to work with potential customers to evaluate the technical feasibility of your idea or design and we can advise on materials, tooling and likely set-up costs.
Q. What are the advantages to have my parts manufactured locally?
A. WinWin Mold can offer quick reaction times to any changes in specification, batch size or material. We can ship small or large quantities anywhere in North America, Europe overnight to accommodate unforeseen changes in demand.
Q. My components have already been developed on CAD. Can you use the drawings?
A. Yes! DWG, DXF, IGES, Solid works and STP, X_T files can all be used to generate quotes, models and mould tools - this can save time and money in producing
your parts.
Q. Can I test my idea/component before committing to mould tool manufacture?
A. Yes, we can use CAD drawings to make Prototype models for design and functional evaluations or market test.
Q. What type of plastic is best for my design/component?
A. Materials selection depends on the application of your design and the environment in which it will function. We will be happy to discuss the alternatives and suggest the best material.
Q. What type of mould tool do I need?
A. Mould tools can be either single cavity (one part at a time) or multi-cavity (2,4, 8 or 16 parts at a time). Single cavity tools are generally used for small quantities, up to 10,000 parts per year whereas multi-cavity tools are for larger quantities. We can look at your projected annual requirements and recommend the
best tooling option for you.
Q. OK, I've decided to go ahead with my project. How long will it take to get my parts?
A. It can take 3 to 6 weeks to have the mould tool manufactured depending on the part's complexity, size and the number of impressions/ cavities (single or multiple). After we receive your final approval on the tool preliminary design, you can expect delivery of T1 parts within 3-6 weeks. And during mold building process, mold build Weekly Update will be provided to you every week for your better understanding of the manufacturing progress in our work shop.
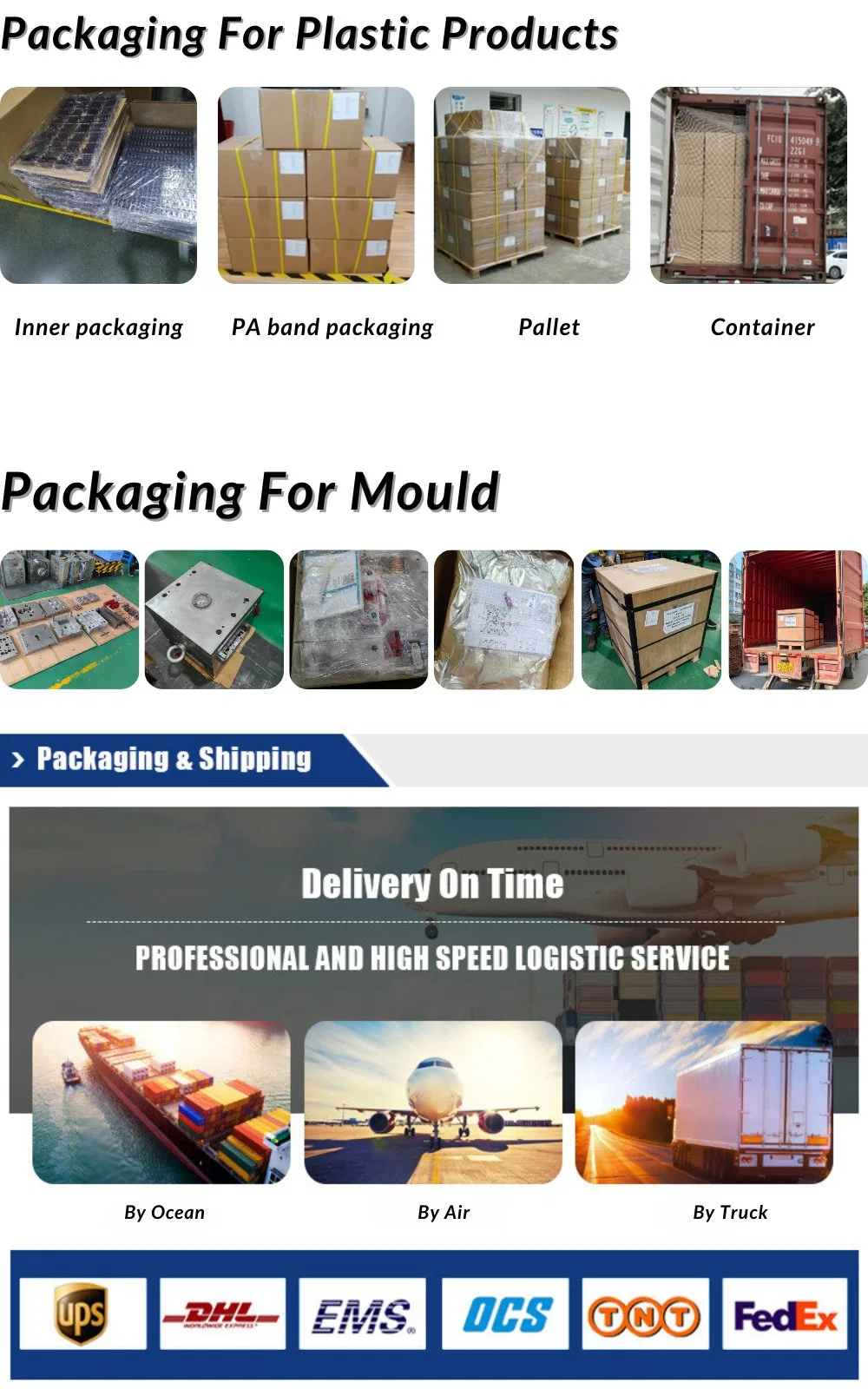