- Overview
- Product Description
- Detailed Photos
- Injection Mold Making Steps
- Our Mould Production Process
- Certifications
- Packaging & Shipping
- Company Profile
- FAQ
Basic Info.
Packaging & Delivery
Product Description
Cap Mould Manufacturer
RJ Mould is specialized in plastic bottle cap manufacturing. We are good at different types of caps, includes Flip top caps mould, Mineral water cap mould, Screw cap mould, Jar lid mould, Pull-push cap mould, 5 gallon bottle cap mould, Oil bottle cap mould as well as other custom cap injection mold.
At RJ Mould, the available cap mould cavity number is from one cavity up to sixty-four cavities. We will suggest the suitable cavity number according to customers' cap design and injection machine size.
Process of Cap Mould Manufacturing
1. Bottle Cap Design
2. Cap Mould Design
3. Cap Mould Manufacturing
4. Cap Mould Trial
5. Water Leakage Testing
6. Mould delivery
Why RJ Mould for Plastic Cap Injection Molding?
We understand that the mould quality is the top concerns for all customers. Keeping that view in mind, our team focus on every steps from mould design, making and delivery.
Our factory always adopst high strength steel material to make bottle cap mold. The hardness of steel is generally more than HRC45. We use high-speed CNC machining center to process molds and carry out standardized operations, to ensure the accuracy of the parts of each bottle cap mold and achieve the interchangeability of each part.
During the mould manufacturing poried, we will report and update the mould status every wekk to customers. And we have a reputation for always meeting deadlines and dlivering mould on time.
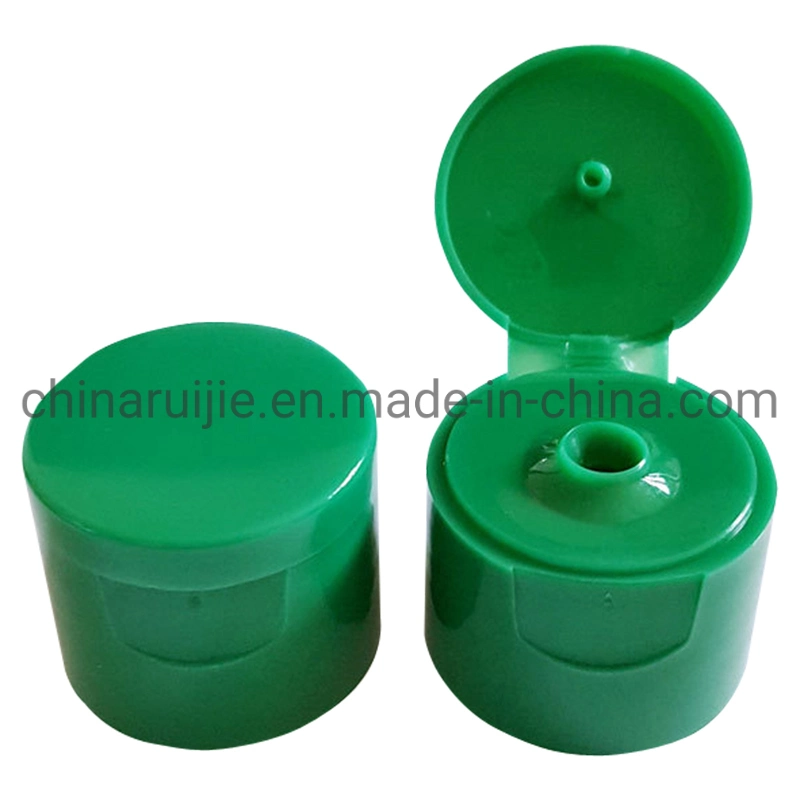
Plastic flip cap mould
Other Plastic Bottle Cap Moulds
Our PET Preform Moulds
The basic steps involved in making an injection mold:
Regular maintenance and optimization of the injection mold are essential for ensuring its longevity and performance over time. This may involve cleaning, lubricating, and inspecting the mold components, as well as making any necessary adjustments or repairs to maintain optimal functionality.
Overall, making an injection mold requires careful planning, precision machining, quality assembly, and thorough testing to create a reliable and high-performing tool for producing plastic parts efficiently and accurately. Collaboration between design engineers, machinists, and moldmakers is essential throughout the process to ensure successful outcomes.
Our factory has already been related to plastic injection mold area for more than 15 years.
If you have any plan to make a new injection mold, or you want to make your own plastic injection pieces with customized design, please don't hesitate to contact us.
1Q: Are you trading company or manufacturer ?
A: We are factory and located in Taizhou City, Zhejiang Provice, China.
2Q: What kind of service do you offer?
A: We can make all kinds of plastic injection moulds. Customized mould project are also welcomed in RJ Mould.
Besides, we have our own injection machine and can do mass production for customers too.
3Q: What information is required for a quote?
A. Please provide us with product 2D or 3D drawing.
If you don't have drawings on hand, samples are also available for checking cost.
4Q: Can I have my own design?
A: Yes, we are very capable to do customized design and make for you. Please share with your ideas, we will discuss your needs, purpose and objective thoroughly and work together with you for the whole project.
5Q: How long is your delivery time?
A: The lead time of T0 sample depends on the mould structure, and generally it takes 20-70 days from receipt/approval of final drawings, deposit and mold design approval.
Mass production delivery time depends on the order quantity.
6Q: What's your payment condition?
A: For Mould: T/T, 40% Deposit with P.O., balance before shipment. Or 100% irrevocable LC at sight.
Part molding: 50% after PO confirmed, 50% after production finished.
7Q: What Hot Runner Brand will you use?
A: As per customers' demands, we can offer YUDO or Chinese local brand hot runner system.
8Q: What's your injection mould life?
A: 0.5 to 3 million shots guarantee, depends on your needs.
9Q: What's the shipping cost? And how long it takes for shipment?
A: Please let us know,
1. Shipment method, do you prefer by sea or air?
2. Destination port or door to door address with ZIP code.
We will check and find the best price for you.